GGML: Safety is not just PPE and protocol, it’s a culture shift
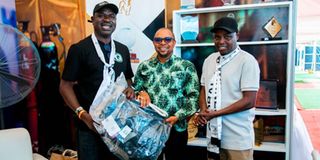
Minister of State, Prime Minister’s Office- Labour, Youth, Employment and People with Disabilities, Ridhiwani Kikwete receives a dummy prize awarded to GGML staff for standout performance in health and safety compliances.
Geita. If you spend enough time around Tanzania’s large-scale mining towns, you’ll quickly learn that the real gold isn’t just what’s pulled from the ground.
It’s in the systems — the people who return home and join their families unscathed, the data that tells the truth, and the quiet, consistent push for something better. Geita Gold Mining Limited (GGML) is trying to rewrite what that looks like in Tanzania.
Forget the boilerplate “safety is our top priority” statements pinned on reception walls. GGML has turned safety into something tangible — even bankable.
“We view the future of safety through two lenses: the use of modern technological systems and the promotion of safe communities. Our participation in OSHA 2025 reflects our commitment to both,” said Dr Kiva Mvungi, GGML’s Senior Health, Safety and Environment Manager while adding: “Digital and AI tools are important, but ultimately, people drive change. That’s why our focus remains on ensuring technology is used to enhance human safety, not replace it.”
In its efforts to enhance and strengthen workplace health and safety, GGML has established a system of providing incentives — including various items and sometimes cash rewards to employees who report potential hazards in the workplace.
Additionally, the company recognizes and rewards outstanding performance by employee safety representatives annually.
You read that right: not just a pat on the back, but a real financial nod to those who choose vigilance over shortcuts.
This incentive system may seem generous, but it’s backed by numbers. GGM has observed a marked reduction in incidents since implementation.
Workers have become more proactive in identifying risks. Hazard reporting is no longer a bureaucratic ritual but a daily ritual of protection.
It starts with the basics — inductions, toolbox meetings, and the deceptively simple “Take 5” protocol, where workers pause to assess risk before beginning a task. This culture of caution is reinforced by a structured escalation system.
Within 24 hours, all incidents that result in significant harm to people or property must be reported to the relevant government authorities.
This reporting system ensures that such events are promptly communicated to both employees and relevant government institutions responsible for overseeing mining operations.
The aim is to promote transparency, accountability, and swift action in addressing safety concerns within the mining sector.
This system isn’t just paperwork. It’s how an organization learns. It feeds directly into risk assessments and site-level adjustments. It ensures that today’s oversight doesn’t become tomorrow’s headline.
While some companies import entire health and safety manuals from Europe or North America, GGML has taken a different route. It localizes best practices — translating technical documents into Swahili, integrating local examples in training, and anchoring procedures in Tanzanian workplace culture. That’s not just smart; it’s sustainable. This practice is addition to the available government standards and regulations.
At the same time, GGML keeps its systems tight. Quality assurance on health and safety is a non-negotiable. Routine and surprise audits ensure that equipment, personnel, and processes all conform to the same expectations.
This attention to detail covers everything from chemical handling to fatigue management — a surprisingly overlooked risk in 12-hour shifts.
There is an ergonomic plan in place, dust and noise monitoring systems active, and scheduled medical check- ups available for staff. Even the water is tested, and the food vendors are monitored for safety compliance.
Contractors who are often critical and important to the mining operations — are looped in with equal seriousness.
This ensures that no contractor claims ignorance when it comes to safety protocols, and no unsafe worker sneaks through under another company’s banner.
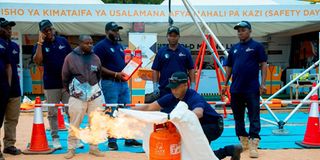
An emergency response officer, Eliamsuri Kawiche from Geita Gold Mining Limited (GGML) demonstrates proper fire outbreak management techniques during the Occupational Safety and Health (OSHA) exhibitions in Singida Region.
All this is beginning to show results. In 2025, GGML has recorded zero fatalities to date. The number of first-aid incidents dropped from ten in 2024 to just two. Medical-treatment injuries were completely eliminated.
“Our goal is to carry out gold mining operations in a way that safeguards lives. That’s why we are here at this year’s OSHA exhibition — because at GGML, safety always comes first,” he said.
Dr Mvungi also highlighted GGML’s recognition as a global leader in safety, having won global safety awards for four consecutive years since 2019 to 2022.
He attributed this achievement to the company’s strong investment in modern systems, including ground fire suppression using foam-based technologies to protect workers, mining equipment and the environment.
These are not stats to be thrown around lightly in a region where many extractive firms still see incident reporting as a public relations risk rather than a health metric.
But perhaps the most striking shift is how the community has been folded into the safety conversation.
Geita isn’t just a mining town — it’s a place where families live, children play, and farmers tilt land not far from high-risk zones.
GGML consults community representatives before new projects launch, and when there’s a spill or an emergency, local residents are now part of the response system. This has been possible because GGML has a system to train and raise awareness to the community members in relation the health and safety emergencies.
Some act as radar keepers, reporting unsafe practices. Others advocate for better standards. It’s a different dynamic: more democratic, more grounded.
The company’s safety framework is aligned with AngloGold Ashanti’s 2030 Aspirational Goal — to achieve a work- place that is free from injury and harm.
It’s an ambitious plan anchored on four pillars: leadership that enables, people who act, systems that anticipate, and technology that eliminates.
Major Hazard Control Standards form the backbone of this framework. These standards do more than list potential dangers; they prescribe controls, demand verification, and require that front-line workers understand what protection looks like in their context. It’s a strategy meant not just to reduce accidents but to kill the idea that harm is inevitable.
And recognition matters. GGML’s safety culture isn’t all hard hats and checklists. The company hosts quarterly and annual HSE award events that honor departments and individuals who model best practice.
These are not vanity exercises. They serve as a mirror — reflecting where the culture is strong and where it still needs reinforcement.
You could argue that this level of detail — from food safety to pre-mobilization protocols — is overkill. But you’d be wrong. Because in mining, proactiveness is often the difference between a routine day and a tragic headline.
Through its strong performance, GGML demonstrates that Tanzania has qualified experts capable of managing health and safety in mining to both national and international standards.
With the time-honoured experience of over 30 years in the mines operations, the company has relentlessly learnt best practices along the journey to become a reckoning force we adore today.
This recognition further highlights that GGML, a Tanzanian company, upholds national and international standards in health and safety.