Achieving cost efficiency objective in an organization
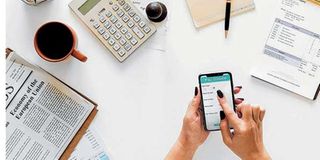
Sourcing Manager gets more credits when he manages a splendid portfolio of suppliers with transparency in spending, efficiency and cost saving.
Considering technological advancements in supply chain field and the increase in number of suppliers, a sourcing Manager might face some challenges in meeting the cost saving/efficiency objectives.
Below are some sourcing techniques that can help the sourcing manager meet his/her cost efficiency targets.
1. Purchase Straight from the Source/Manufacturer.
Globalization has made product manufacturers far more reachable than they previously were. There was a time when manufacturers dealt only with wholesalers. Now companies and normal people can deal with manufacturers directly rather than buying from retailers.The benefit of dealing with manufactures is the assurance of getting original products. Manufacturers are the pundit in their own products, they know in detail about the product and you get firsthand knowledge about the item you are purchasing.This reduces or eliminates middlemen. And manufacturers often stock a larger quantity of products compared to retailers.
2. Purchase from authorized dealers
Not all Companies are as big as Toyota/Continental/ Apple / Samsung – to name a few; which are based globally. Other companies are not globally–big, so they have authorized dealers to locations and regions where they don’t have physical presence. This is the second best way in making purchases for an organization. However, if you want to purchase a commodity/item /spare part or anything, first search from the website customarily to find list of their authorized dealers which are in your region/country.
3. Costing and assimilate in duties, taxes and importing regulations.
Costing has to be planned before any purchase is done by first comparing prices from different suppliers. Costing should start from the price of the item, Freight Charges, profit margin, miscellaneous, Taxes, to the selling price. Be well informed about how duties and taxes are calculated, how and when they are to be paid. This is the best time to peruse more on TRA, TFDA, TBS Website pages. All of these data have to be accurate in order to get beneficial outcome to the organization.
4. Inventory management
Inventory management simply means specifying the shape and placement of stocked goods. You can stock up to a year worth of goods if your inventory management corresponds with your budget and clients consumptions.
Thus simplifying your sourcing as it can only be done twice – thrice a year. Invest in supplier management software for detailed, accurate and up to date inventory information.
5. Avoid “spoon-feed”
It is oddly common to hear someone say, “It is cheaper to purchase from dealers instead of ordering one from abroad.”
And if you ask if he/she knows by figures how expensive it is to import goods/materials, they usually do not know.
Most of the time people/sourcing managers are being spoon fed information about how expensive it is to import goods or materials And often one is too lazy to actually take time to learn whether it is true that ‘importing is expensive’ We live in a world where technological advancement is at its peak, for official or personal use, you can buy anything from anywhere – You just have to be well informed on how to do it.